Contact Us
Does your pulp mill primarily use chlorine dioxide to meet brightness targets?
Using too much ClO2 has unintended—and negative—consequences.
When it’s time to make a decision about the pulp bleaching process, operators will always choose brightness over other objectives. It’s a reasonable position. Who wants to spend the time, money and effort to rework or dispose of pulp that doesn’t meet customer expectations? But the common remedy of overfeeding comes at a cost—well beyond the price of the chemical itself.
Every additional pound of chlorine dioxide used means that much energy is spent cooling and heating water, as well as the production of more AOX in the discharge of your effluent. It also means more hazardous rail cars to unload and more residual threatening your people.
Additionally, ClO2, the most selective of the conventional bleaching chemistries, is not perfect. While it’s oxidizing the chromophores, it’s also oxidizing—and thus damaging—the wood fiber itself. This leads to lower viscosity/less fiber strength. When ClO2 is the only tool you have for achieving brightness, you end up making compromises that hurt your business.
What if you could reduce your dependence on chlorine dioxide?
Chlorine dioxide usage—particularly overfeeding—does have negative side effects. By using Buckman’s Vybrant® technology, you will use less ClO2 and still achieve the same brightness results. The most immediate impact is you can reduce your chlorine dioxide chemical spending by up to 20 percent—without making any additional capital investments.
Using less ClO2 brings a host of additional benefits. It means less water to cool and heat, reducing your energy costs and your carbon footprint. Fewer pounds of ClO2 also leads to less AOX discharge, allowing you to get ahead of emerging regulations, such as Ecolabel in Europe. You can take a proactive stance towards the environment. At the same time, you do less damage to the integrity of your wood fiber, yielding better pulp viscosity and strength. Finally, you cut the amount of hazardous chemicals handled by your people—those used to make ClO2 and ClO2 itself—as well as reducing the potential for off gassing. The resulting increase in safety means more than dollars—it means peace of mind.
Achieve better ClO2 efficiency.
You want every pound of chlorine dioxide to move the brightness needle as much as possible. By using Buckman’s Vybrant technology, you make this happen.
Using Vybrant before the addition of ClO2 allows you to remove bulk chromophoric groups off the surface of the fiber, including lignin fragments and Hexanuronic acids. By removing these elements, you reduce the work that must be done by the chlorine dioxide, allowing you to use less of this chemical. You will also remove many of the materials on the outside of the fiber that are not chromophores but would interact with—and consume—chlorine dioxide needlessly. This opens up reactive sites at the fiber surface, allowing more chlorine dioxide to penetrate and do its job properly. Finally, after your bleaching process, you can utilize Vybrant again to remove remaining chromophores to achieve even higher brightness and make the pulp bluer based on L,a,b Value measurements, reducing the need for expensive dyes on the paper machine, all without purchasing any additional equipment or infrastructure.
All this means you can use less chlorine dioxide and achieve the same brightness results—reducing chemical and energy costs. In the process, you produce a pulp with less fiber degradation, less toxic effluent, and less potential worker exposure to hazards. You improve across the board.
Have you already tried enzymes for pulp bleaching and they didn’t work?
Ten to fifteen years ago, some mills attempted to use enzymes to aid the bleaching process. But there were problems back then. These early Xylanases were not pure products and contained fair amounts of cellulases which could cause significant pulp degradation.
Yesterday’s Xylanase-based enzymes could only tolerate a narrow pH range—between 7.0 and 7.2. But most mills operate in the 8.5 to 11.0 range. To get the pH down so the enzymes could work, you had to apply acid. This added cost and complexity to the process. Even if you could drop your pH level, due to natural fluctuations in the mill, it was difficult to keep it within this tight 7.0 to 7.2 band. But this was just the beginning of the drawbacks.
When you add acid to your brownstock, it releases the sulfides in the form of hydrogen sulfide gas—an extremely hazardous material. The sulfuric acid used can also corrode equipment—which was not designed to handle such a dangerous material. This can lead to spectacular failures and unexpected capital costs.
Additionally, when you artificially drop the pH, it causes the chromophores, lignin, and hemicellulose to form a shell around the fiber. And this inhibits effective bleaching. Sometimes, you couldn’t add enough ClO2 to get the required brightness. Additionally, many mills also experienced higher COD levels in their effluent because of this process.
As a result of all this, the common perception was that enzymes were not worth the headache.
What if you could continue to operate at the mill’s natural pH and use enzymes?
Enzyme-enhanced bleaching can deliver significant value, but only if it can work in your mill. By partnering with Buckman, you can employ enzyme technology without pre-treating your pulp. You remove the need for a costly and complex acid-based pH-reduction process, making it easier to conduct initial trials in anticipation of moving to full production. You’re able to change your organization’s opinion of enzymatic technology for brightness. And once you’re up and running, you will realize the benefits of reducing chlorine dioxide usage—cost, sustainability, yield, and safety—without any of the negative side effects experienced in the past. Through this modern approach, you achieve the brightness you need in a simple and cost-effective way.
Vybrant has a higher and broader pH tolerance than its competitors.
Deploy advanced enzyme technology without jumping through hoops: You don’t want to fuss with your pH if you don’t have to. When you use Buckman’s Vybrant technology, you can realize all the benefits of our enzymatic technology for brightness and still operate up to a pH of 10.2. By taking advantage of the highest pH available for a bleaching Xylanase, you avoid any disruption to your process and incur no additional capital costs. Buckman will work with your operators to learn how to take full advantage of this breakthrough chemistry. And as Buckman works to increase Vybrant pH tolerance levels even further in the future, you will have even greater freedom to operate your mill in the way you want. Only with Buckman will you find this degree of pH tolerance—in terms of both range and absolute level. As a result, your bleaching operations will be simple, cost-effective, and safer.
With Vybrant Enzymatic Bleaching Technology, your mill can:
Speed up production.
- Hit brightness targets more easily without worrying about ClO2 generation limits.
- Eliminate bottlenecks caused by a stressed ClO2 generator chiller system in summer months.
- Increase production by raising the Kappa number in the digester while reducing load at the recovery boilers.
- Improve pulp yield, adding incremental tons to your output.
Improve pulp quality.
- Target hemicelluloses and Hexanuronic acids, allowing your ClO2 to bleach to a higher final brightness with less reversion.
- Add stability to the process, reducing chances of off‑grade pulp.
- Make the pulp bluer based on L,a,b Value tests and reduce usage of optical brightener and dyes on the paper machine.
Reduce costs and environmental impact.
- Reduce ClO2 to save money, stay in compliance and protect the environment.
- Cut the volume of water processed through the bleach plant.
- Reduce usage of other bleaching chemicals such as caustic and hydrogen peroxide.
- Lower energy use (less chilling and reheating of CIO2).
- Minimize AOX discharge.
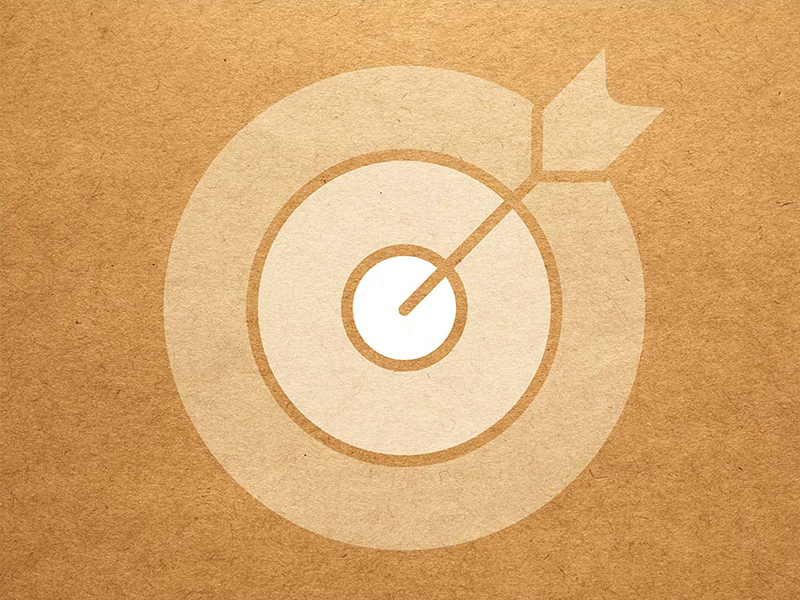
Hit pulp brightness targets with Vybrant
With Vybrant pre-bleach enzymatic technology your mill can hit pulp brightness targets using less chlorine dioxide, water and energy.
LEARN MORE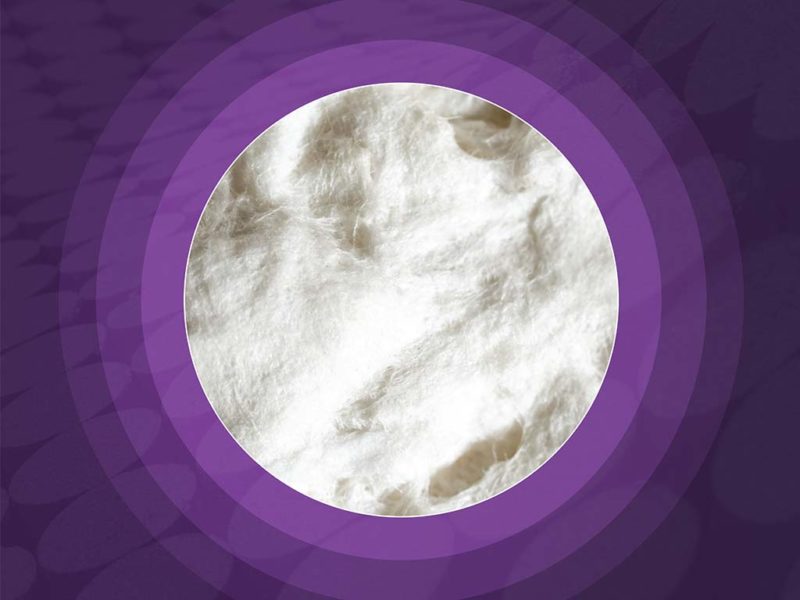
Reduce ClO2 and Reversion with Vybrant Post-Bleach Technology
Vybrant 900 series technologies use specially selected enzymes to remove chromophores in bleached pulp, reducing ClO2 usage and reversion.
LEARN MORE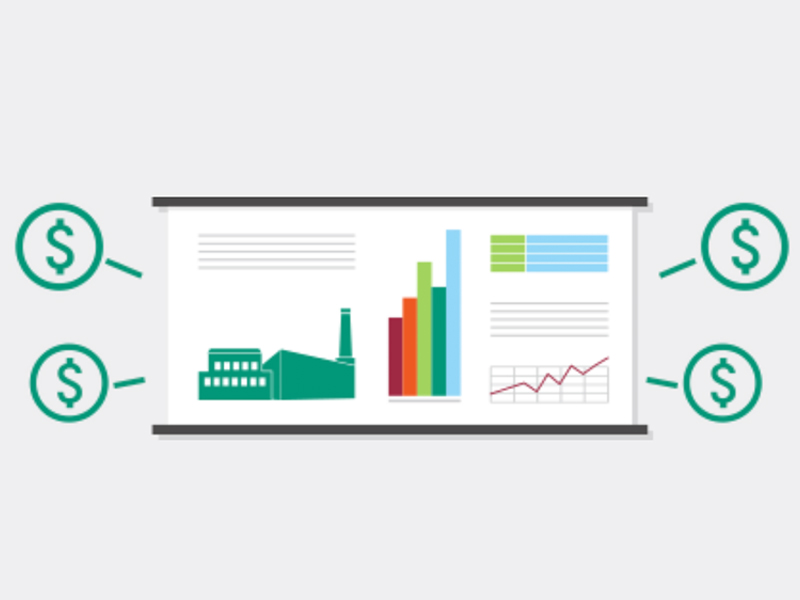